Protecting crowns improves fruit quality for Sellars Bananas
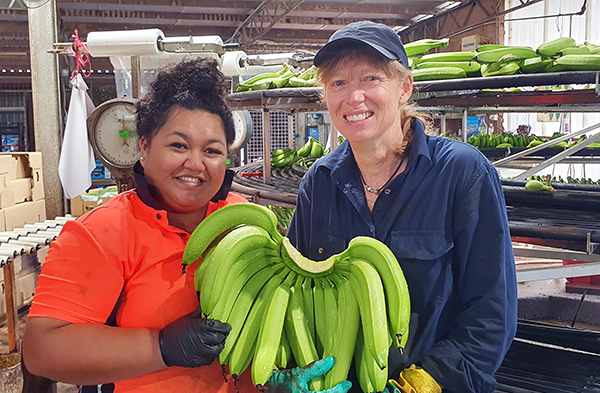
Sellars Bananas are renowned for producing premium quality bananas. However, frustratingly, even when supplying the best quality fruit at the farm gate, fungal organisms can wreak havoc with consignments down the supply chain. This has been the recent experience of Sellars Bananas and feedback from market agents is, they are not alone.
Crown end rot (CER) is caused by several fungal species and symptoms develop on the cut surface of the crown. Symptoms can differ in terms of severity depending on the causal fungal organisms present. Less severe damage includes superficial white/fluffy fungal growth on the cut surface. These symptoms rarely progress into the fingers of the fruit or affect eating quality (Figure 1). However, the more severe form of CER, commonly known as Chalara results in a black rot that extends from the crown into the fruit stalk and into the fingers, severely impacting fruit quality (Figure 2).
Feedback from the market is that CER continues to be a problem and symptoms start to develop as the fruit is ripened. It is hard to pick up before fruit is sent to retailers as not all cartons may be affected, and it may only impact one or two clusters across several cartons in a consignment. The good news is, there are post-harvest fungicides registered for use in bananas that can control CER.
Naomi Brownrigg from Sellars Bananas shares their experience with the problem and what they have put into place to manage it.
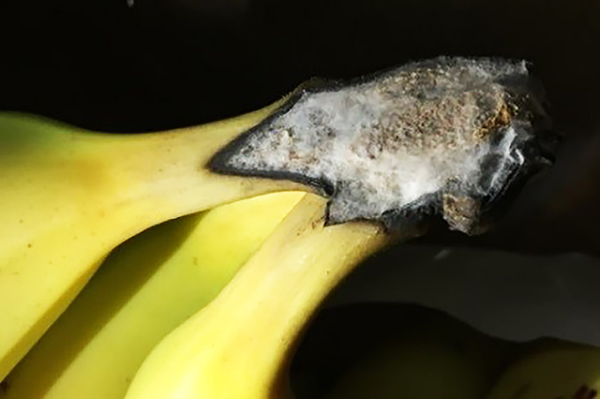
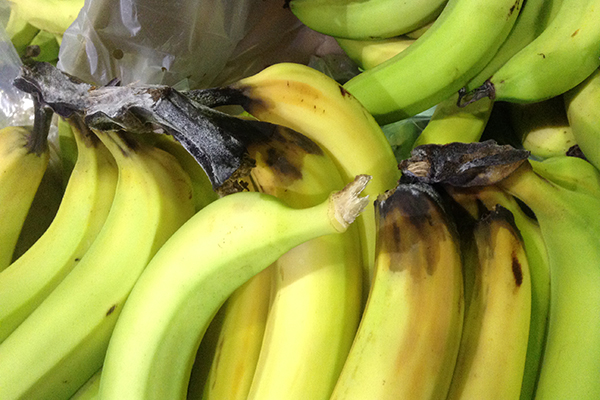
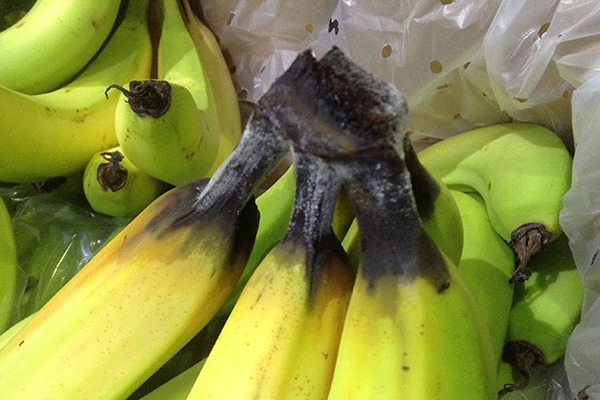
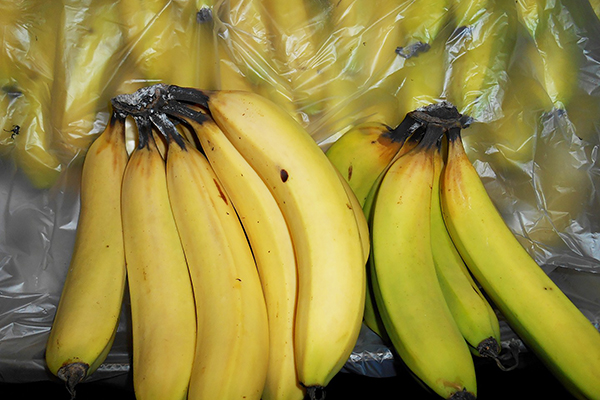
Chalara, a recent issue for Sellars Bananas
The symptom of superficial fungal growth on the cut surface of crowns has always been a minor problem from time to time for Sellars Bananas, predominately in the summer months. Naomi became more concerned when she started to see symptoms of Chalara approximately 3 years ago, causing more significant damage to fruit quality. ‘We never thought we had to treat it until Chalara started to turn up. At first, it was just now and then in the winter months, and then it started to appear most weeks of the year over a period of 2 years,’ Naomi said. ‘If you have never seen Chalara, it’s like CER on steroids. It will quickly rot the fruit from the crown down once the ripening process begins. Not all cartons are affected, it may be only one or two boxes or some clusters in a single box.’
Good shed hygiene and the use of chlorine didn't fix the issue
Before implementing the post-harvest spray system, Sellars Bananas tried different practices to resolve the issue. ‘Initially, we tried sanitising the shed and used a high-pressure cleaner in all of the wet areas. Although it’s a good practice, it didn’t work,’ Naomi said. ‘We then tried an inline chlorinator that used chlorine tables, that also didn’t work. Finally, at the congress last year, I spoke to Kathy Grice and David East from the Department of Agriculture and Fisheries on the issue and they were pretty clear that the only way to control it was with a post-harvest spray. So, we set about implementing a post-harvest fungicide spray, using prochloraz that treats all the fruit on the wheel.’
The packing wheel required some family ingenuity
Naomi enlisted the expertise of her brother-in-law Mark Nissen to come up with a spray system that would work for their 3-tier banana wheel (Figure 3). Once they had designed the frame at the right height and angles, Mark welded the steel frame together. The next step was attaching the spray system. ‘We set up a spray rig with three nozzles, one for each tier on the wheel, and attached a 200 L Silvan tank to it with a spray unit (Figure 4),’ Naomi said. ‘The spray unit puts out 7 L/min and each nozzle puts out 300 mL/min. The pressure is regulated, and any excess chemical solution is returned to the tank.’ As per the label instructions we do not catch any of the solution from underneath the wheel once it has been sprayed on the fruit. We use the product Protak® and the label rate is 110 mL/200 L. For our operation, this means we are using 250 mL of Protak® each day.’
Tips for placement of spray booths:
- Spray booth should be placed after the fruit wash.
- Position spray nozzles and clusters to ensure the crown surface is sprayed (Figure 5).
- Set the speed of the wheel or belt (trough systems) to allow a 30-second spray.
- Position the spray booth at the furthest point possible away from packers and use spray shields to minimise spray mist (Figure 6).
- Place spray booths in a well-ventilated area.
Have a trough instead of a wheel?
Many packing sheds have installed post-fungicide spray booths, spraying crowns after they leave the trough and before reaching packers.
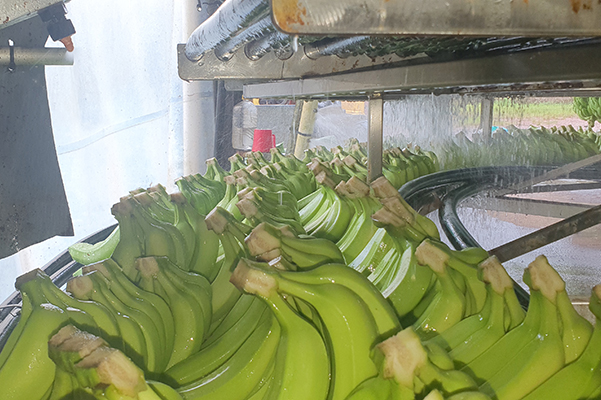
Implementation didn't require changes to existing practices
No changes were required in terms of Sellar’s packing procedures. ‘We were already placing the fruit with the crowns up,’ Naomi said. ‘There seems to be no mist from the spray, as there is a protective shroud around the spray unit (Figure 6). We are using Protak®, so there is no smell, and our packers all wear gloves.’
The benefits outweigh the cost
All up the cost of the spray unit itself excluding labour, was approximately $2000. This includes the tank, pump, inverter, hoses, nozzles, connections etc. and steel for the frame. The only ongoing costs apart from electricity costs for the pump, is the chemical itself. ‘We average one litre of Protak per week and current pricing is $170/L,’ Naomi said.
Although Chalara was the main reason for Sellars to implement a post-harvest spray, they believe the benefits have been substantial when it comes to overall fruit quality. ‘The difference it makes to the appearance of the crowns at the market is huge, you can store the fruit for longer knowing that the crowns are going to hold up which gives them options as to when the fruit gets sold,’ Naomi said. ‘You may think this is a bad thing, but if the crowns are not holding up, that fruit needs to be sold ASAP, sometimes at a discount. I have been told that buyers of our fruit are very happy with the results. I wish we had implemented it (spray system) years ago.’
Sellars’ market agent is also happy with the results and now sends Naomi photos of clean crowns since they have installed the post-harvest fungicide spray (Figures 7 & 8).
If you would like more information on this case study or managing CER in bananas contact DAF’s Banana Extension Team via email betterbananas@daf.qld.gov.au.
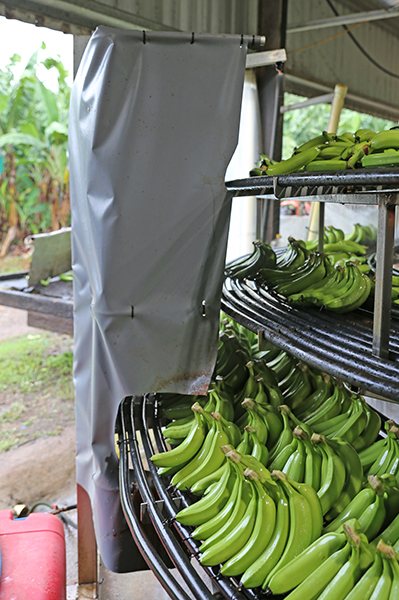
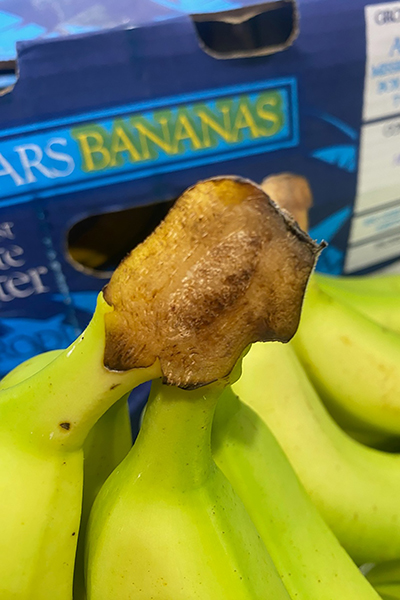
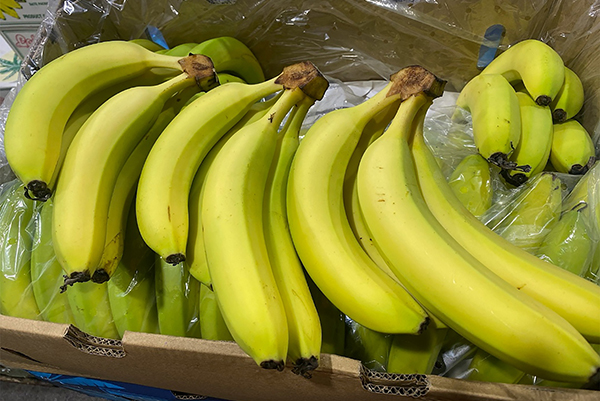
Thank you
Thank you to Naomi Brownrigg and the team at Sellars Bananas who provided their time and gave permission to use this case study for the benefit of the wider industry.
The application of post-harvest fungicides is the most effective management strategy.
Research led by Kathy Grice from the Department of Agriculture and Fisheries (DAF) has shown that post-harvest fungicide application is the most effective management strategy. At the time of publication products containing thiabendazole (e.g. Tecto®) and prochloraz (e.g. Protak®) are registered for post-harvest use in bananas. Important screening work undertaken by DAF has shown that some of the organisms that cause CER are less sensitive to thiabendazole-based products, particularly in the coastal regions of Far North Queensland. These organisms remain more sensitive to products containing prochloraz.
The application method is different depending on what product you use.
Products containing thiabendazole (e.g. Tecto®) are registered for use as a dip. Whereas products containing prochloraz (e.g. Protak®) are registered for use as a non-recirculating spray system only.
Always check the APVMA website for the registration status of products before use and follow label directions.
More information
This case study has been produced as part of project BA19004 the National Banana Development and Extension Program which is funded by Hort Innovation, using the banana industry research and development levies, co-investment from the Department of Agriculture and Fisheries and contributions from the Australian Government. Hort Innovation is the grower-owned, not-for-profit research and development corporation for Australian horticulture.

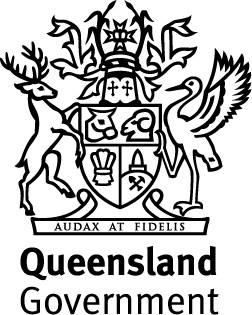